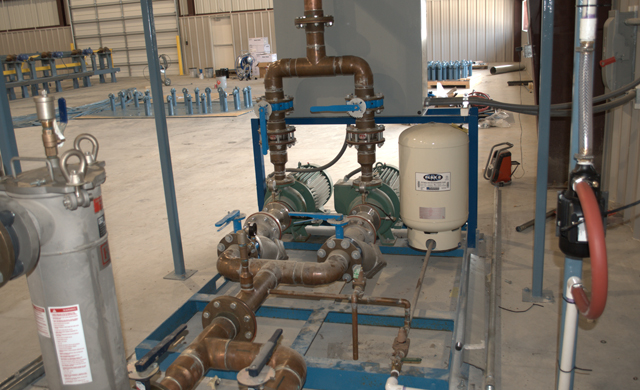

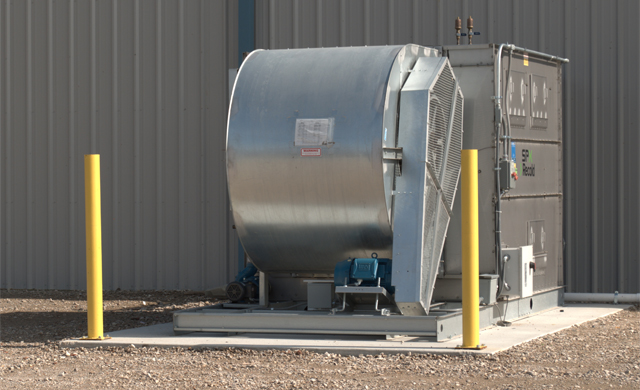


Induction use for tempering of pipe is a controversial subject. Although the practice is used successfully on general pipe it is not as successful when the pipe is a thicker wall or the grade is a high strength. The argument that are made by some metallurgists is that lack of full uniformity can cause some issues. In addition they argue that although the conversion is made there needs to be some time at temperature for crystal growth. The better solution for increased soak time would be a tunnel furnace but the best solution is a walking beam furnace.
The induction process is the absolute fastest way to put energy into a tube, pipe or bar. ESG utilizes induction in some of its designs to take advantage of this remarkable feature. Induction allows a shorter process line and may reduce capital costs.
As with all positives, there can be some significant negatives that need to be accounted for in the decision. The largest penalty when utilizing induction is the energy cost. The overall process uses less Btu than a furnace utilizing natural gas but the low gas prices that we are experiencing provide a substantial cost per pound savings. Future gas price are predicted to remain low due to the abundant supply while energy costs are predicted to rise as consumption continues to climb.
Induction coils are designed based on the diameter of the pipe to be heated. The coil needs to be coupled closely with the outside pipe diameter in order to provide good efficiency. When more than one diameter pipe are used in the same coil the efficiency will be less because the distance to the surface is different.
A second consideration in induction design is the frequency. Typically the heating occurs slightly below the surface. A certain amount of time is required for the inner diameter to reach the same temperature as the outside diameter. Thicker wall pipes are worse. Lower frequency will cause the heating to occur deeper into the body. This can help to some degree with thicker pipe. The frequency normally is fixed.
If the induction coils are not properly staged the heating will not have time to equalize and the temper will not be uniform. Induction heating is usually staged with multiple coils to allow the heat to equalize. We recommend to utilizes a short inline furnace after the induction to provide the soak for both a more uniform body and and better crystal growth. This can improve properties and save energy.
The following is typical of induction heating of pipe.

Electric versus Gas cost analysis
The following analysis provides an analysis based on a specific location utilizing real electric and gas pricing
The energy penalty for electric can be greater than $100 per ton Click here for the details.